Zu wissen, was geschieht, bevor es geschieht, ist ein alter Menschheitstraum. Gerade im Bereich von Maschinen- und Betriebsführung wäre es sehr wertvoll, wenn man die Zukunft vorhersagen könnte. So würden Betriebsaus- und unfälle komplett vermieden werden. Leider gehören Zukunftsvorhersagen nach wie vor in den Bereich der Fantasie. Was aber heute schon zu den Zeiten von Industry 4.0 sehr nah an Hellseherei herankommt ist die Technik der Predictive Maintenance und Condition Based Maintenance.
Dieser Artikel soll eine Übersicht über die Vorausschauende Wartung bieten und zeigen, wo man die Industrie 4.0 Predictive Maintenance gewinnbringend einsetzen kann.
Sie möchten mehr darüber erfahren, wie Sie mit vorausschauender Wartung Zeit und Geld in Ihrem Unternehmen sparen können? Kontaktieren Sie uns für ein unverbindliches Beratungsgespräch!
Dieser Artikel beantwortet folgende Fragen zu Industrie 4.0 Predictive Maintenance und Predictive Maintenance Machine Learning
- Welche Vorteile bietet predictive Maintenance?
- Was versteht man unter Industrie 4.0 Predictive Maintenance?
- Wo fordert Predictive Maintenance Machine Learning Algorithmen oder Deep Learning for Business und welche Rolle spielt Big Data?
- Was sind die Voraussetzungen um Predictive Maintenance einsetzen zu können?
Was ist predictive Maintenance und was sind die Vorteile?
Predictive Maintenance nutzt die Daten vor Ort sowie Cloud-Computing, um das Zeitfenster für die Planung von Wartungsarbeiten zu erweitern. Durch moderne predictive Analytics Verfahren kann man nicht nur den aktuellen Zustand von Industrieanlagen zentral und nahezu in Echtzeit beurteilen, sondern auch den zukünftigen Zustand vorhersagen. Somit können die Lebensdauer von Maschinen und mögliche zukünftige Probleme prognostiziert werden.
Auf diese Weise können Unternehmen Produktionsausfälle und Arbeitsausfälle reduzieren. Dadurch wird wertvolle Zeit für Maschinen und Mitarbeiter im Unternehmen freigesetzt. Durch die Kosteneinsparungen beim Budget für Instandhaltung werden zudem zusätzliche Mittel für beispielsweise Forschung und Marketing frei. Kurzum, die wirtschaftlichen Vorteile von predictive Maintenance für Industrie 4.0 Unternehmen sind beträchtlich. Tatsächlich hat McKinsey geschätzt, dass durch vorausschauende Wartung die Wartungskosten um 10 bis 40 Prozent gesenkt werden können.
Gerne stehen Ihnen unsere Experten zur Verfügung. Wir freuen uns, mit Beratung zu Predictive Maintenance, Predictive Modeling und Predictive Analytics zur Ihr Unternehmen voranzubringen. Wir erklären anschaulich und anwendungsorientiert die Möglichkeiten und Optionen für vorausschauende Wartung für Ihr Unternehmen. Nehmen Sie Kontakt auf! Wir freuen uns auf ein Gespräch.
Industrie 4.0 Predictive Maintenance
Ein Beispiel: Wenn man sich Montag morgens ins Auto setzt, um zur Arbeit zu fahren, und der Motor dann nicht anspringt, ist das verheerend. Denn der Ausfall von Gerät, wenn man es eilig hat, ist besonders ärgerlich und kann zu weitreichenden Problemen führen. Hätte man das Auto aber am Samstag zur Werkstatt gebracht, wäre die schwache Batterie wahrscheinlich aufgefallen und ausgetauscht worden. Die Fahrt zur Arbeit am Montag wäre dann kein Problem gewesen. Aber woher sollte man am Samstag schon wissen, dass die Batterie am Montag den Geist aufgibt?
Bei KFZ ist gesetzlich eine vorbeugende Instandhaltung (oder Preventive Maintenance) vorgeschrieben. Dies bedeutet, dass man in bestimmten Zeitintervallen gewisse Wartungen durchführen und Teile austauschen muss. Die Zeitintervalle basieren auf empirischen Erfahrungswerten und sind mit viel Sicherheitspuffer geplant. Dadurch werden häufig Teile getauscht und Kosten verursacht, wenn dies noch gar nicht nötig gewesen wäre.
Würde man aber das KFZ durch Sensoren jede Sekunde seiner Existenz sehr genau beobachten, wäre man in der Lage Änderungen im Ladestrom der Batterie zu entdecken und diese gezielt, wenn es zeitlich passt, kurz vor dem Ausfall zu tauschen. Dies nennt man in der Industry 4.0 Condition Based Maintenance. Man überwacht dabei jede Maschine, jeden Prozess an allen möglichen Punkten live dank Mikroelektronik mit Sensoren. Die ausgelesenen Daten vergleicht man mit Normwerten und bei Abweichungen über einem bestimmten Grenzwert werden automatisch Wartungen angeordnet.
Der Nachteil von Condition Based Maintenance
Condition Based Maintenance weist aber weiterhin den Nachteil auf, dass man schadhafte Teile zwar erkennen kann, bevor größerer Schaden entsteht, aber es ist dennoch eine reaktive Art der Instandhaltung. Somit diktieren immer noch die äußeren Umstände den Zeitplan für die Wartung. Um wirklich vorhersagende Instandhaltung, also Predictive Maintenance zu erreichen, fehlt ein weiterer Schritt.
Sollten Sie professionelle Unterstützung für Big Data Predictive Analytics Big Data benötigen, helfen unsere Statistiker Ihnen gerne weiter. Kontaktieren Sie uns einfach für eine kostenlose Beratung & ein unverbindliches Angebot.
Predictive Maintenance Machine Learning
Industrie 4.0 Predictive Maintenance setzt nämlich modernste Machine Learning Prozesse ein, um vorherzusagen, wann Instandhaltung notwendig werden wird. Wie das funktioniert, verdeutlicht die folgende Grafik:
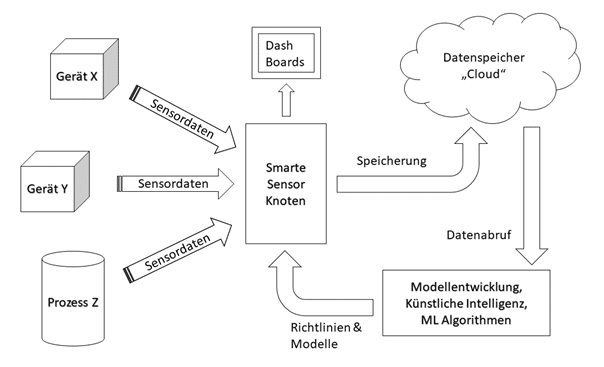
Bei Predictive Maintenance spielt die Entwicklung von Modellen durch künstliche Intelligenz die zentrale Rolle. Denn die unfassbar hohe Anzahl an Sensoren, die die Maschinen und Prozesse überwachen, produzieren täglich viele Gigabyte an Daten. Ein Mensch wäre gar nicht in der Lage, diese Daten zu sichten. Geschweige denn, sie zu analysieren und Modelle daraus herzuleiten.
Smarte Sensorknoten übernehmen hier die erste Analyse aller Daten, erstellen daraus Grafiken, treffen Entscheidungen und leiten die Datensätze schließlich an die Cloud weiter. Von hier haben Supercomputer darauf Zugriff und können anhand der Datensätze Modelle entwickeln, mit denen man Ausfälle mithilfe statistischer Methoden vorhersagen kann. Diese Predictive Maintenance Machine Learning Modelle werden dann in die smarten Sensorknoten eingepflegt, wo sie als Grundlage für Instandhaltungsplanung dienen. So wird Vorausschauende Wartung Realität: Anhand der in Echtzeit aufgenommenen Daten und der durch das Real Time Reporting entwickelten Modelle kann man vorhersagen, wie der Zustand der Geräte und Prozesse in den nächsten Tagen und Wochen sein wird.
Wie funktioniert predictive Maintenance?
Predictive Maintenance bietet datengestützte Erkenntnisse über das Auftreten von Ausfällen. Eine entscheidende Rolle spielt dabei die Anomaly Detection (zu deutsch Anomalieerkennung). Anomaly Detection ist eine Technik des maschinellen Lernens und kann die Wahrscheinlichkeit künftiger Ausfälle vorsagen. Das Verfahren kann dabei Entscheidung treffen, welche auf Daten über kritische Werte, Risikovorhersagen sowie Ausfall- und Wartungskosten basieren. Wenn eine kritische Schwelle erreicht ist, löst die Analyse eine Warnmeldung aus, damit entsprechende Maßnahmen ergriffen werden können.
Dabei stützt sich die Überwachung auf eine Unzahl von Sensordaten. Einige dieser Sensoren messen beispielsweise:
- Temperatur
- Druck
- Vibrationen
- Drehgeschwindigkeiten
- Chemische Eigenschaften des Schmieröls
Messwerte über oder unter den Normalwerten können dabei zukünftige Probleme signalisieren:
- Erhöhte Temperaturen können zum Schmelzen oder Verbrennen von Komponenten führen und müssen je nach Ausrüstung behoben werden, bevor sie signifikante Schäden verursachen.
- Die Schwingungsanalyse könnte Einblicke in mögliche Ausfälle bieten, da starke Vibrationen Anzeichen für das Versagen von Komponenten sein können.
- Auch durch die Analyse des Schmieröls kann man abschätzten, ob sich der Zustand einer Maschine verschlechtert. Dabei wird beispielsweise die Menge an Verunreinigungen und der Verschleißabrieb im Schmiermittel gemessen. Vor 50 Jahren benötigte man für diese Analyse noch die Expertise von Tribologen (Experten für Maschinenverschleiß). Inzwischen werden Daten über das Maschinenöl automatisch durch IOT extrahiert und entweder direkt durch IOT oder im Labor analysiert. Dadurch lassen sich detaillierte Verschleißmuster ableiten.
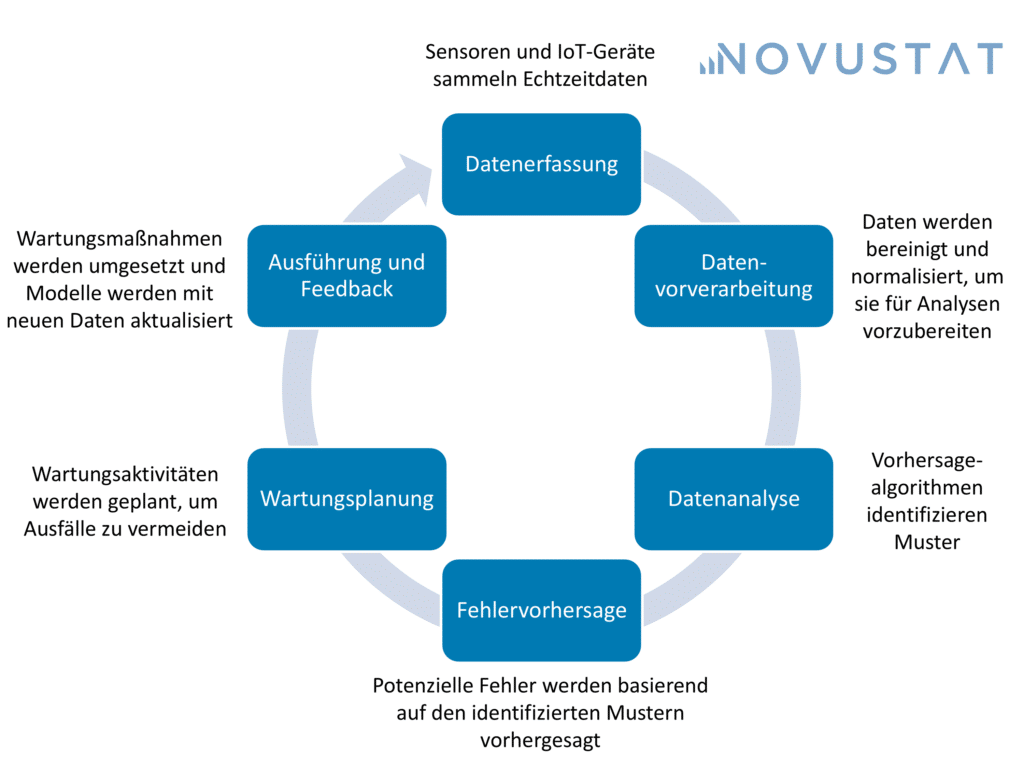
Das Real Time Reporting solcher Variablen ermöglicht ein sofortiges Eingreifen. So können Probleme gelöst werden, bevor sie überhaupt entstehen. Weiterhin kann eine Zeitreihenanalyse abnormale Abweichungen aufzeigen. Solche Abweichungen würden bei einer isolierten Betrachtung akzeptable
Praxisbeispiele zur Predictive Maintenance
Praxisbeispiel 1: Predictive Maintenance in der Automobilproduktion
Ein Automobilhersteller nutzt Predictive Maintenance, um seine Produktionsmaschinen zu überwachen. Sensoren an den Maschinen erfassen in Echtzeit Daten zu Vibration, Temperatur und Betriebsdauer. Diese Daten werden in der Cloud gespeichert und durch maschinelles Lernen analysiert. So kann das System bevorstehende Wartungsbedarfe erkennen und rechtzeitig eingreifen, bevor eine Komponente ausfällt. Diese Vorausschau minimiert Produktionsausfälle und spart Kosten, da Wartungen nur bei tatsächlichem Bedarf durchgeführt werden.
Praxisbeispiel 2: Condition-Based Maintenance in der Öl- und Gasindustrie
In einer Ölraffinerie werden Pipelines und Kompressoren kontinuierlich durch Sensoren überwacht. Die Sensoren messen Temperatur, Druck und chemische Eigenschaften der Rohrinhalte. Die gewonnenen Daten werden analysiert, um Anomalien zu erkennen, die auf einen möglichen Defekt hindeuten könnten. So kann das Wartungsteam auf Basis der Sensorwarnungen präventive Wartungen durchführen, bevor größere Schäden entstehen. Hierdurch sinken die Betriebskosten und das Risiko von Produktionsstillständen.
Die Chancen: Durch predictive Maintenance die Vorteile von Cloud und IIoT nutzen
Predictive Maintenance bietet allerdings noch weitere Chance für produzierende Unternehmen. Unternehmen, die sich predictive Maintenance zunutze machen, werden in der Lage sein, ihre Produkte wesentlich agiler zu produzieren und anzubieten. Mit einer intelligenten Fabriksentwicklng kann vorausschauende Wartung die Geschwindigkeit und Anpassungsfähigkeit in der Produktion deutlich erhöhen und die Kosten signifikant senken. Durch predictive Maintenance werden somit moderne Industrie 4.0 Konzepte wie As-a-Service- oder Pay-per-Use-Angebote mit ihren komplexen Produktionsprozessen oft überhaupt erst möglich. Die Fertigung kann somit kundenorientierter geschehen und neue Einnahmequellen können erschlossen werden.
Ausblick: Was kommt nach predictive Maintenance?
Wir erwarten, dass in Zukunft einige Unternehmen sogar noch über predictive Maintenance hinausgehen und sich eher um prescriptive Maintenance bemühen werden. Dieser Ansatz verwendet prescriptive Analytics und strebt eine vollständige Automatisierung an. Dabei werden Machine-to-Machine (M2M) Techniken angewendet, damit Maschinen ihre eigene Wartung für sich selbst planen können.
Produzierende Unternehmen mit teurer Ausstattung werden vermutlich jedoch zunächst immer noch menschliche Kontrolle in ihrem System haben wollen. Damit dass Potenzial der digitalen Transformation voll ausgeschöpft werden kann, müssen Unternehmen daher nach technologischen Lösungen suchen, die kompatibel mit ihren Mitarbeitern sind. Gleichzeitig wird es auch in Zukunft von entscheidender Wichtigkeit sein, stets mit den neuen Technologien und Trends Schritt zu halten.
Voraussetzungen für Predictive Maintenance
Predictive Maintenance weist allerdings einige Anforderungen an Betriebe auf. Zum einen sollte schon Technologie der Industry 4.0 vorhanden sein. Dies bedeutet vor allem, dass man alle Maschinen und Prozesse mit modernsten Sensoren überwachen sollte. Die erhobenen Daten müssen sauber voranalysiert werden und in geordneten Datensätzen auf Datenbanken gespeichert und abrufbar sein.
Außerdem ist es auch entscheidend, wie viele Maschinen der gleichen Art ein Betrieb verwendet. Denn für aussagekräftiges Predictive Maintenance Machine Learning ist es notwendig, dass in den Datensätzen auch Fehlfunktionen und Ausfälle aufgenommen worden sind. Gibt es keine Daten über solche Zwischenfälle, oder gibt es von jedem Gerät nur eines im Betrieb, dann ist die Datenlagen nicht ausreichend, um Industrie 4.0 Predictive Maintenance anzuwenden.
Fazit
Solange jedoch die oben genannten Punkte erfüllt sind, steht nichts im Weg, sich näher über die Vorausschauende Wartung zu informieren und die Produktivität und Prozessstabilität auf das nächste Level zu bringen. Novustat bietet bei Bedarf eine ausführliche Beratung zu diesem Thema – kontaktieren Sie uns!
Predictive Maintenance hat bereits damit begonnen, die Prozesse in der Fertigung zu revolutionieren. Predictive Analytics ist die entscheidende Schlüsseltechnologie, damit Unternehmen die vollen Potenziale der Cloud und von IoT ausschöpfen können.
Für die Einführung von vorausschauender Wartung bedarf es zum einen natürlich einer professionellen Datenverwaltung. Weiterhin muss man aber auch flexible Prozesse schaffen, die das gesamte Spektrum von Datenquellen, Werkzeugen und Systemen zusammenführen. Nur so kann man eine nahtlose Interaktion zwischen Daten und Menschen sicherstellen.
Unternehmen, denen es aber gelingt predictive Maintenance erfolgreich einsetzen, erhalten nicht nur den Zugang zu ungeahnter Zeiteffizienz, sondern auch zu völlig neuen Arbeitsweisen und Ansätzen in der Fertigung. Gerne begleiten wir Sie auf diesem Weg!
Weiterführende Links:
Industry 4.0 beim Bundesministerium für Wirtschaft und Energie